In my previous article I made the case for the significant advantages that engineered wood products (EWP) from a plantation grown forest brings.
Wood is a spectacular and clever evolutionary wonder, where trees use sunlight to convert carbon dioxide into a trunk that is simultaneously light, flexible and strong. Strong enough for a tree to hold many tons high enough to be above its neighbour (worlds tallest tree is 116 meters high – equivalent to a 35 story building), flexible enough not to blow over or be snapped by the snow and ice and light enough to be pushed very high.
All we need to do is utilise this strength and lightness and flexibility and we can build tall stable low cost buildings that lock away tons of carbon dioxide at a time. We don’t need to manufacture building materials we only need to utilise what we have been given naturally. It seems improbable that we can do a better job than what 700 million years of evolution has refined and optimised.
The dream that my business partners and I brought to this insight was to build a factory that could emulate the strength of a plantation grown Radiata pine tree into every piece of wood product manufactured from it, in a low impact sustainable manufacturing system. Our solution is to create building materials produced in small-scale highly automated factories located adjacent to forests in a process that uses renewable bio-energy to make it all happen.
The realisation of this dream could then lead to a number of great outcomes. Forestry economics would be substantially enhanced from supplying a reliable and high value use of Radiata pine logs in New Zealand. Furthermore, with our current business model underperforming, primary industry regions in New Zealand could see economic development and higher paying jobs. New Zealand as a whole could experience the benefit of adding value to one of our greatest natural resources.
You could describe our dream as achieving the economic and social trifecta of winning in wealth creation, regional economic and social development within an innovation that mitigates against the scourge of global warming. The odds might have seemed long but the prize looked huge. It was therefore worth betting our resources on, and we did!
Fast track to today and we’re off to the races, the first prototype Optimised Engineered Lumber (OEL™) plant is under construction on the outskirts of Gisborne, thanks to the full support of the Eastland Community Trust, Callaghan Innovation, Scion and some forward thinking people. The first (of many) OEL™ plants will by the end of 2017, be selling high grade structural wood compliant with the NZ building code and all NZ standards, and which will utilise all of the recoverable wood out of 85% of the tree’s full stem. The waste wood, such as sawdust, chip and bark is captured and used to provide all the energy required to power the kilns, heat set the glue and generate electricity to run the machines. Being next to the forest the emissions are available to be reabsorbed by the trees that grow more wood for processing the next year, and so on.
For those of you with more of an engineering and process interest let me explain what is going on. One meter logs are cut by automated sawmills into a single and uniform stick weighing 2.25kg each after drying. The sticks are guided through a process where they are each individually tested for strength, then finger jointed together into a 6-meter length. The 6 meter finger jointed pieces are laminated together in a continuous press in a specific way that replicates the strength characteristics of the original tree into a single piece of OEL™. It’s really that simple. Every part of the log serves a purpose in the tree stem and each stick in a piece of OEL™ serves an analogous purpose in its new configuration. A log at the start of the process is transformed into many pieces of structural, glue laminated, engineered wood product (EWP) just 6 hours later and ready to be sent to a building site. This process is fully automated but managed by high value technical workers using a method that advances not only efficiency but also health and safety avoiding human contact with the wood and cutting machinery.
The OEL™ EWP that is delivered by this production system is designed to achieve a specific strength characteristic analogous to the inherent strength found within the original log and tree stem that it was re-engineered from. The EWP is an analogue of the original tree, with a known strength and a low level of variability. OEL™ arranges the wood in a similar pattern to where it would have been in the original tree. Our building material makes effective use of the original log and efficient use of the total resource in the waste to energy process that drives the entire production system.
Many other benefits are possible by the OEL™ EWP process. Alternative species to Radiata with different inherent characteristics can also be processed separately or mixed to produce a combined product that further refines the quality such as strength or stiffness. Using this approach it is even possible to harvest young trees rather than those at full term rotation while still achieving the required strength characteristics. Logs that are bent, curved or too small to process through a conventional sawmill or peeler mill can still be utilized as OEL™ feedstock as the 1 m log length “straightens out” the curves and any log down to a meter is still usable. Larger cross section posts and panels for walls and floors can be fabricated by combining OEL™ or implementing simple changes to the production system.
The OEL™ process begins with a small log and immediately converts the material into very small and uniform dimensioned pieces of wood produced quickly on small scale machinery. The manufacturing plant is small when compared to any other log processing operation and is significantly lower cost to build. Consequently it becomes economical for small plants to be distributed around the forest, located where the logs are rather than trucking logs to large and centralized plants. The bioenergy process also allows the plant to operate off an electrical grid or other energy reticulation system like gas or even geothermal.
Another advantage for plants localized at the forest is that high paying jobs are established in those regions. The pay-rate for the approximately 50 people that will work in a full scale plant will reflect their higher level of training and qualification and be double that of a conventional sawmill. The wealth effect in the region is one attractive thing but perhaps even more beneficial is that the opportunity will attract workers back home for good paying jobs when a primary reason they don’t live there now is the absence of work in the first place.
OEL™ has the potential to change the way we look at forestry, redefine how we build low and high rise structures, enhance employment opportunities in the regions and positively contribute to how we can look after our planet.
The Future is here
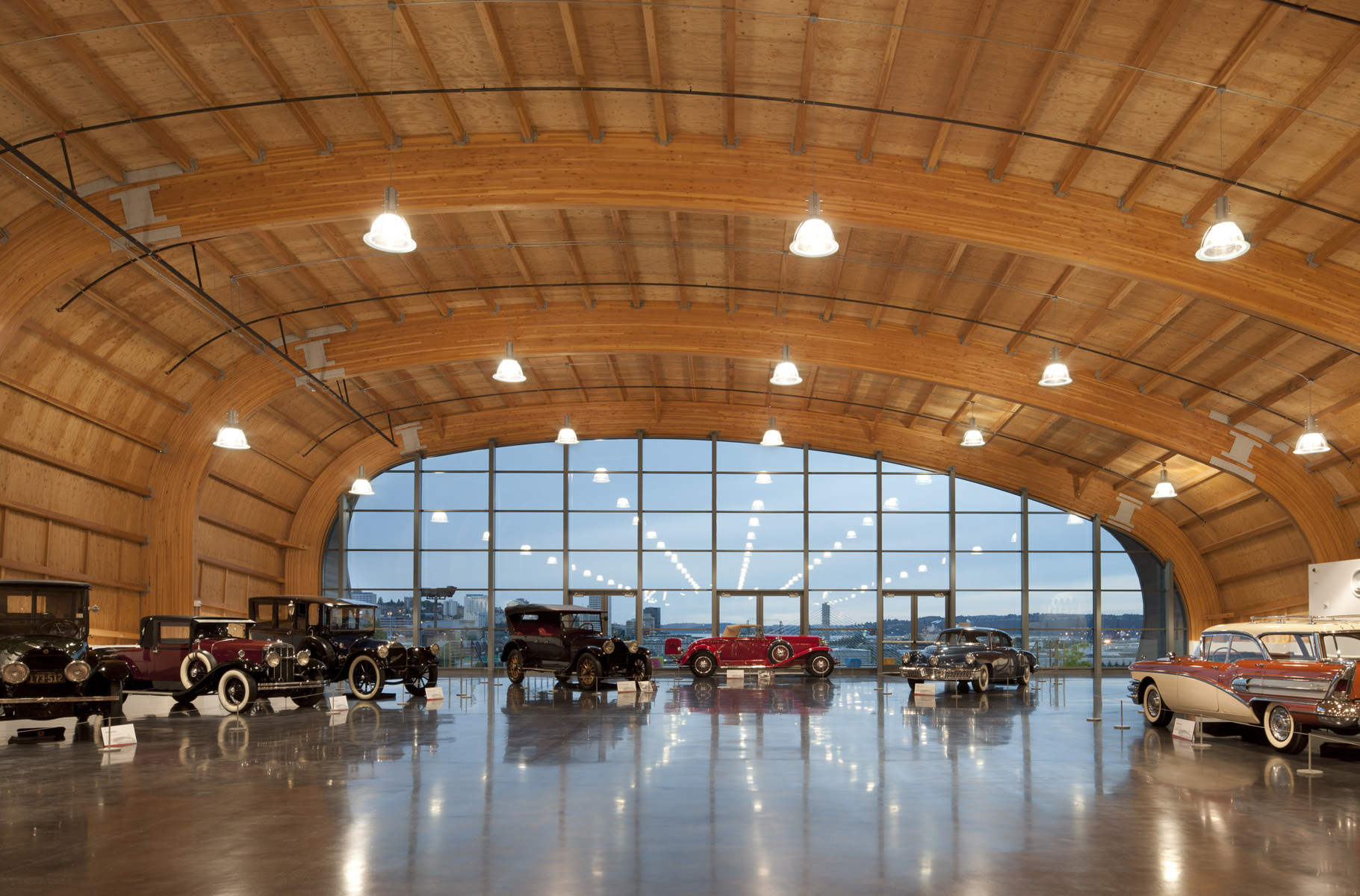
The LeMay Car Museum
Convincing arguments for timber as a viable alternative to conventional materials and methods for buildings that continue to trample the planet with giant carbon footprints. OEL™ is demonstrating that wood is actually the optimal material for economically sustainable construction.
Anders Berennsson, the Swedish architect who has designed Tratoppen, a 40-floor residential wooden tower on the drawing board for construction in Stockholm, is quoted in the September 16th edition of the Economist magazine as saying engineered wood will become the cheapest way to construct tall buildings in the future. We agree with Mr. Berennsson but suggest that the future is already here with OEL™.
An exciting development is underway that will supply sustainably produced light weight, high strength, flexible building materials to a waiting market, creating jobs in urban areas, enhancing the economy and improving the environment.
Leave a comment