As New Zealand heads into what is being anticipated to be the largest period of home building in its history, with 40,000 homes per annum expected over an extended number of years, the question is raised as to where we will get the resources necessary to make this happen.
Resource categories critical to successfully achieving the plan include:
- Land resources to build on
- People resources to construct
- Building material resources to construct with
- Utilities to service the buildings
- Furnishings and equipment to provide habitability and
- Capital to pay for it all. Needless to say, the plan will not be achieved if the “Resource Requirement Plans” have not been thought through and implemented well.
At the start of a major undertaking is the best time for the community to take the opportunity, not only to decide on how to achieve the plan efficiently and on time but also, and even more importantly, to make sure that what is being done is in alignment with our best outcomes, that is to say it will also be an effective plan.
Before the start is the best time to also consider the options available to achieve our broader societal aspirations. In the case of entering into a very large construction phase, society can consider its aspirations around quality of life generally, protection of the environment that we have to occupy, equity and social cohesion. This article is then about how some prudent choices now, can enhance the outcome of these loftier objectives and should be considered carefully at this particular juncture.
I will confine the question to our options around the building materials we use and why it is a very good idea for us to pivot strongly towards the use of wood as our building material of choice. The production and use of wood is a smart choice for New Zealand and this is true on numerous dimensions. To use more wood we will need to concentrate on engineered wood products (EWPs), which combine all the significant advantages of wood, with all the characteristics of strength, stability, durability and performance of steel, aluminium, concrete and plastics.
Why should we want to build with wood?
We are now well aware that the concentrations of carbon dioxide and other heat trapping greenhouse gases are increasing in the atmosphere as we burn more fossil fuel, and that these gases are accelerating global warming, by trapping long wave radiation reflected from the earth’s surface.
We can reduce the release of fossil carbon dioxide into the atmosphere by simply reducing the use of steel, concrete, aluminium and plastics and increasing the use of wood. Steel, concrete (or rather the cement content of concrete), plastics and aluminium all require more energy for their manufacture than wood and in addition to the energy required to manufacture these materials, the primary processes involved in their making also adds to atmospheric carbon dioxide.
Steel is made from iron that begins as iron oxide. On reduction, this produces iron and carbon dioxide. Cement is made by heating clay and limestone together – limestone is a fossil carbon, calcium carbonate. In this process, which involves a kiln heated to 1500 °C, limestone is reduced to calcium oxide to form an aluminosilicate mixture. The Greenhouse gas carbon dioxide is a by-product that is released into the atmosphere. This carbon dioxide is not reabsorbed when cement is used in concrete.
To properly compare this with wood we also need to address the question of wood’s ultimate breakdown. Does wood, on its eventual burning or decay, become a greenhouse gas? By using more wood then are we merely delaying the atmospheric release of carbon?
It is true that the carbon in wood eventually becomes atmospheric carbon dioxide. However there is a very important difference. The carbon released from fossil fuels remains, for millions of years, a permanent addition to the atmosphere. Provided however, that the wood comes from a sustainably managed forest, the equivalent amount of carbon to that which is released into the atmosphere is removed again, within a few years to grow more wood. The carbon from wood use recycles the considerable atmospheric carbon locked away in the plantation forests. The use of fossil fuel however, together with the chemical reduction of metal ores and the production of cement, permanently increases the atmospheric carbon dioxide greenhouse gas level.
Much rigorous scientific work has been done around the world and here in New Zealand, on what the scholars have termed the “emitted carbon” that comes from our building materials and therefore our built structures. The notion being worked on is the laudable goal of how to minimize the carbon “footprint” of a building over its lifetime, through the judicious choice of building materials. Wood is a store of carbon, rather than a carbon emitter.
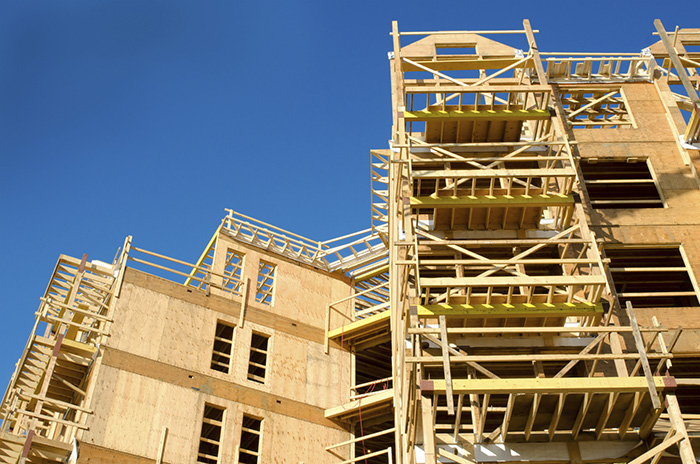
Wood Frame Construction Site
The use of wood in building locks away that carbon store for the lifetime of the building. A sustainably managed plantation forest, standing behind the buildings, that continuously supplies the building materials, is itself storing approximately 300 tonnes of carbon per hectare from the air. Each hectare of plantations therefore stores away again the carbon released in driving an automobile for 1.5 million kilometres. Remembering that there are 1.7 million hectares of plantation forest in New Zealand, that is the sequestering of carbon dioxide from 10 million cars driving a quarter of a million kilometres each. Another author on this platform, David Hall, has suggested that we in NZ should grow another 1.3 million hectares of forests, on unproductive land, and I agree with this proposition but suggest further that sustainably managed plantation forests, on agricultural land, are an even better option.
As opposed to storing carbon, all other building materials emit carbon dioxide when they are manufactured. The following graph gives a useful estimate of carbon emission in the manufacture of one kg of the particular building material, remembering that wood has been naturally manufactured, as it were, from carbon dioxide in the first place. Furthermore, the density of the products is substantially different; a kilo of wood goes further than a kilo of concrete, for example. The second graph shows the relative energy efficiency between wood and other building materials.
When building a home in New Zealand we can note the benefits of utilising wood in two ways. The first is the extension of the carbon stored in plantation forest into the wooden building materials and secondly, when wood is used it substitutes out of the system the high carbon emitting alternative building materials.
“Wood is very energy efficient. Wood requires a tenth or less of the energy needed to make wood substitutes such as steel and concrete.”
-Dr. W. R. J. (Wink) Sutton International Forestry Report 1999
Building a 250 square metre NZ home with wood, as compared with non-wood materials, is calculated to result in approximately 23 tonnes of carbon dioxide being removed from or not put into the atmosphere. This is equivalent to the amount of carbon dioxide produced by driving any average petrol fueled car for 115 thousand kilometres. So 40,000 houses a year so constructed would remove 920,000 tonnes of carbon – equivalent to that released by driving the said car for 4.6 billion kilometers. At the end of the life of the house (say 75 years) the wood can be recycled, burnt or buried, eventually returning the carbon dioxide to the atmosphere where it can be reabsorbed by the same plantation forests it originally came from to produce again further building materials.
The case for building with wood is, therefore compelling. Why don’t we mandate the use of wood – especially as we approach this new high water mark of building activity? There are of course understandable reasons why this has not happened and why high carbon emitting materials have come to substitute wood out of the build. The impediment to wholesale transfer over to wood arises from what we can think of as constraints, on both the consumption and on the production side. Constraints that are now however very largely overcome by the properties obtained from the previously mentioned EWP class of wooden building materials..
Conventional wood in the form of beams, posts, framing and joinery has been what steel, concrete, aluminum and plastics have substituted out of the building over the last century. The task now is to engineer natural wood in such a way that it can substitute the high carbon emitting substitutes themselves, back out of the building system.
Many EWPs have been developed in recent times and are finding their way into low, medium and high-rise construction. Some of these forms of EWPs are becoming known as “Mass Timber” products and are gaining wider acceptance.
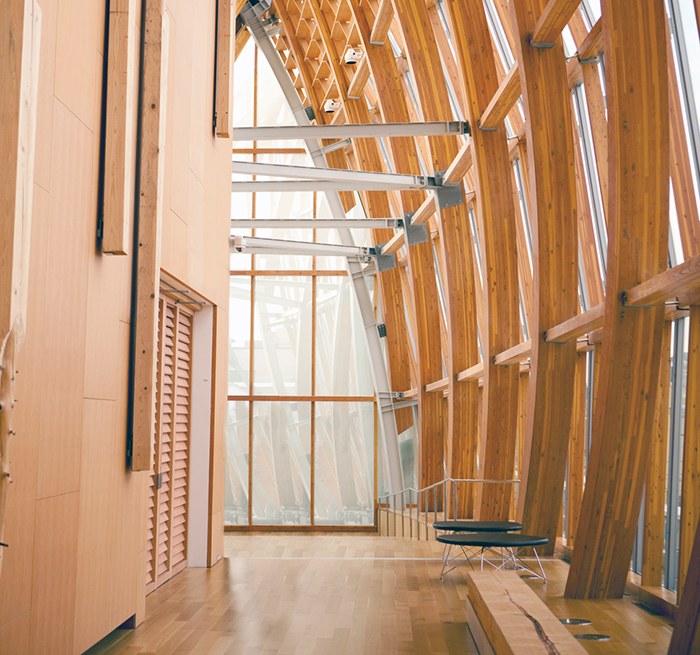
Recycled wood and lumber business interior
What Mass Timber EWP should we use in New Zealand?
A little background on timber is required first. On the consumption side, solid wood (as opposed to EWP and Mass Timber) has a high variability inherent in its make up. Different pieces of lumber from the same log, tree or forest can have quite different performance characteristics from each other.
This variability in the inherent “specification” of wood results in building designers and specifiers opting to use known performance products where, for example, strength is important in a high-rise building. The EWP or Mass Timber materials available therefore need to offer not only strength (and straightness, durability, stability etc.) but also defined levels of such, with only a “small standard deviation about the mean” as the statistician would say. Optimised Engineered Lumber (OEL™), cross-laminated timber (CLT), glue-laminated timber (glulam), parallel-strand lumber (PSL), laminated-strand lumber (LSL), laminated-veneer lumber (LVL) and wood I-joists are good examples of Mass Timber EWPs that provide this surety of performance in their inherent specification.
The use of EWPs however, still remains constrained. This is largely the result of production-related concerns, where: 1) cost of manufacture can be high, 2) only a small proportion of the logs from the tree are suitable for use in these applications, and 3) only a small proportion of the wood from the log itself meets the standard required for it to be used.
Where to from here to unlock the benefits of wood in the built and natural environment?
What is required then, before the vision of substituting the high carbon emitting materials back out of the building system can be practically achieved, is a low cost manufacturing system that can utilise any tree from the forest, uses all the wood available from those logs, with a technology that produces known and defined performance specifications. Such a technology would turn all the sustainably managed plantation forests in the country into resource suitable for building materials that are affordable alternatives to all other building materials, and would hold the critical advantages of having a negative carbon footprint while also being produced in a low carbon emitting manner.
If further to the above, the manufacture of such products could be done close to the forest, then; the energy stored in the waste material from the logs could be used to heat the kiln drying and produce electricity to run the manufacturing process; employment opportunities could be created for skilled workers in those regions where the forests are located where generally it is difficult to sustain high paying employment; and sufficient revenues provided back to the forest owners to make more attractive the investment case for the sustainable operation of the forest. We would then have a profoundly good outcome across all the areas identified earlier; quality of life, protection of the environment, equity and social cohesion.
There are a few technologies already available that go part of the way and one known as OEL™ developed by Wood Engineering Technology Ltd., that achieves all these beneficial outcomes and addresses the production related concerns of other EWPs is being commercialised now in Gisborne. A subsequent article will lay out in greater detail the breakthrough that WET has achieved and the technology at the heart of OEL™.
Now is the time for New Zealand to put work into solving any and all outstanding impediments to utilization of the mass Timber EWP materials so as to get them into the supply chain and resource the upcoming building boom in an optimal way, the best way we know how. Such an opportunity to profoundly change the quality of outcome for society, at such a low cost, is only rarely encountered.
Leave a comment